Employment Opportunity – Plant Personnel
November 6, 2018
When selecting a conventional foam filter, the typical approach is to go with the highest pores per inch that still permits flow. And that is about it. What if you could pick your flow, level of filtration, tighten your tolerances, all in a more durable product that is the same every manufacturing run?
How are Lattice™ 3D Filters Different?
Our filters are 3D printed exactly the same each and every time. This allows us to control the metal flow evenly throughout the filter, providing an engineered, torturous path for the metal. But that is just the most basic benefit, what else does 3D printing allow you to do?
Uniformity of Flow
Instead of a PPI number that tells you little about the performance of the product, we provide benchmark values for flow rate under a consistent head pressure. The graph to the left shows that when using flow as a benchmark our filters are 3-4 times more consistent compared to an industry standard! We do better than just match your current PPI filter.
Additional Filtration
Each shape is 3D modeled to precisely control the printed lattice. This allows for controlled surface area, and manipulation of the Lattice Density for a more torturous path. This increased surface area and a very torturous path provide a higher filtration at a greater flow even with a thinner filter.
Engineered Lattice
There are very few limitations of the design. No need for dual stage filters with a limiting junction, our filter can be manufactured to change from top to bottom, seamlessly blending different filtration levels. Unconventional shapes are easy.
Material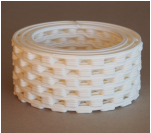
Lattice filters are offered in a high purity 99% alumina. Other materials are available upon request. A common industry issue with foam filters is “snowing” where pieces of the filter break off and end up in your castings. Each strut in our filters are bonded in multiple locations. Not only is this much more durable, but individual strut failure does not result in an inclusion in your castings.